Predictive Vibration Analysis
Vibration analysis can be performed as a predictive tool for investigating the wear condition of rotating components in industrial plants.
Only a thorough vibration analysis can identify which rotating components require maintenance in industrial plants, allowing for targeted maintenance interventions that optimize resources and energy.
CEAR has the appropriate instrumentation to conduct vibration analysis investigations on industrial plants.
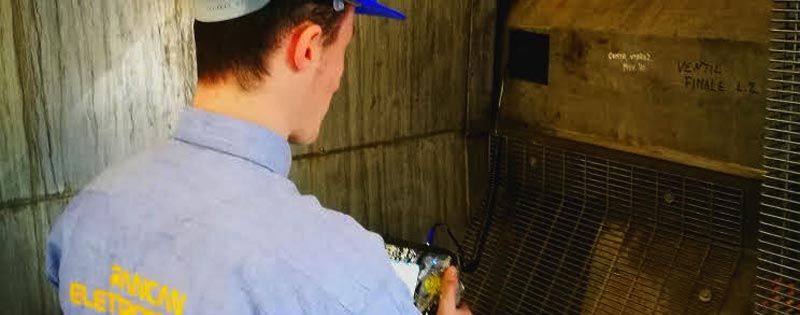
What is the purpose of vibration analysis
The values obtained and the vibration spectra provide a precise functional overview of the electrical machine, highlighting all ongoing wear: from those justified by the operating hours accumulated to those that are already present anomalies (both mechanical and electrical). All vibrations of different frequencies objectively and unequivocally demonstrate the worn component.
Subsequent vibration analysis surveys, if conducted periodically (semi-annually or annually), provide a timeline forecast of the wear evolution of the components, thus establishing maintenance shutdown times before a breakage or failure occurs during production.
With this approach, the intervention planned from the vibration analysis optimizes costs by minimizing unexpected downtime due to sudden failures. Additionally, it precisely identifies which components to maintain or replace, allowing all those with remaining guaranteed operating hours to reach the end of their lifecycle.
What are the results?
The valuable insights extracted from the vibration analysis spectra define mechanical wear (worn bearings, loose supports, motor misalignment of the driven machine, etc.) or electrical problems related to the power supply (harmonics beyond allowable limits) or incorrect inverter supply connected to the driving motor.
Therefore, no resources are wasted on unnecessary or premature maintenance operations: the intervention allows for the timely replacement of worn components or recalibration of out-of-configuration electrical parameters.
We are not just a predictive analysis firm that offers opinions on a problem, but a company that provides both solutions and field operations: starting from a thorough preliminary analysis of the existing vibrations, an operational plan is defined. Upon completion of the intervention, a further vibration analysis is conducted to verify the expected result.
Often, the client requests our intervention to analyze vibrations in a fan deemed excessive, perhaps after having already performed other balancings over time: with our investigation method, the true causes of the imbalance, which go beyond the fan’s own imbalance, become evident. Thus, a resolutive intervention with immediate feedback on the results obtained.
A case study
In a steel mill, an abnormal operating noise was detected in the overhead crane lifting unit for silo loading.
After performing a vibration survey on both lifting motors and the central gearbox, we analyzed the overall vibration spectra at various frequencies to identify all peaks related to gear pairs (engaged gear pairs), specifically detecting one with an absolute value higher than the average of the others.
Using the typical mechanical data of the gears, it is possible, through vibration analysis, to identify if there is a specific vibration for each gear pair and to determine if it exceeds the allowable limits.
In the described case, it was the second reduction pair inside the gearbox that showed not a gear breakage, but greater wear compared to the other pairs. With ample advance notice of a failure and subsequent production stoppage, vibration analysis allowed for the planning of the gearbox maintenance intervention without disrupting normal production.
There were no attempts at unnecessary correction or adjustment, but rather an intervention that involved a limited commitment of human and economic resources to the components in need of care or replacement. Vibration analysis allows intervention before failure, reducing both maintenance and production downtime costs.