Laser Alignment as a Resource Saver
In machine alignment, using a laser aligner means saving on the costs of coupling and bearing replacement, as well as reducing energy costs due to excessive friction from misalignment.
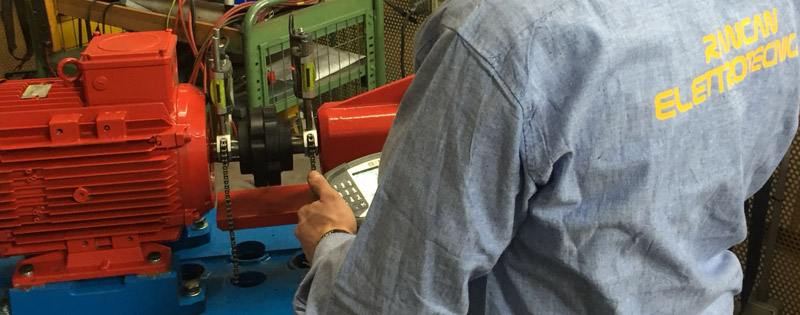
Even though many maintenance technicians still perform alignments (drive motor and driven machine) “manually” with rulers and calipers, laser alignment not only precisely aligns two shafts (or two pulleys) but also identifies if the motor’s four feet are not on the same plane (soft foot). This allows for specific correction of the out-of-plane foot, minimizing possible vibrations during operation. The laser alignment distance can reach up to 10 meters, ensuring precision and corrections up to a tenth of a millimeter.
Laser alignment can be performed on both vertically and horizontally positioned motors. Below are the benefits of using laser optical instrumentation, like ours, for maintenance:
- Extended Lifespan of Coupling Elastomers: Proper alignment reduces stress and wear on the elastomeric elements of the couplings, extending their functional life.
- Reduced Mechanical Vibrations:
- Energy Savings for the Drive Motor: Reduces rolling friction on the bearings, leading to lower energy consumption by the drive motor.
- Extended Lifespan of Bearings: Proper alignment minimizes undue stress and friction on the bearings, significantly prolonging their functional life.
We don’t just perform the mechanical alignment (with report provision); we also test its quality by measuring operating temperatures (coupling and bearings) and the vibration profile. These objective parameters help identify any misalignment between couplings or pulleys.